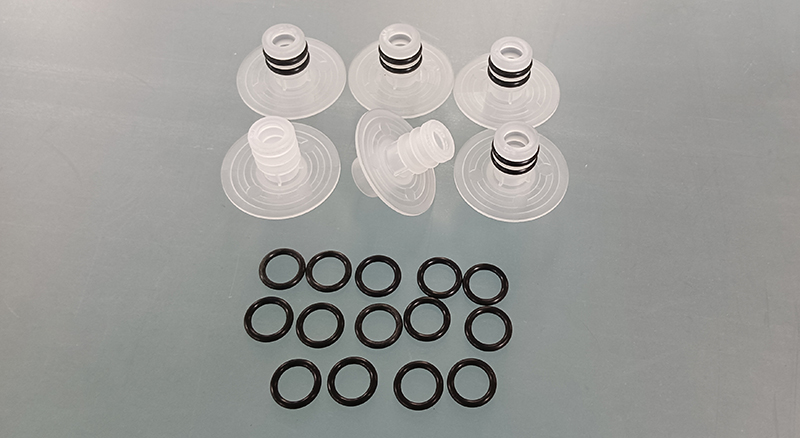
一、O型圈自动化装配设备的主要类型
1.1、全自动压装设备
工作原理:通过气动或伺服电机驱动压头,将O型圈精准压入沟槽。
特点:
高精度控制压力与位移,避免O型圈拉伸或破损;
可集成视觉定位系统,适应复杂工件。
典型设备:伺服压装机、气液增压压装设备。
1.2、推装式自动化设备
工作原理:利用机械推杆或夹具将O型圈推入装配位置。
特点:
适用于对称结构工件(如圆柱形轴类零件);
结构简单,成本较低。
典型设备:推装机械臂、旋转推装工作站。
1.3、真空吸附装配设备
工作原理:通过真空吸盘抓取O型圈,配合精密定位系统完成装配。
特点:
对O型圈无接触损伤,适合高洁净场景(如医疗、半导体);
可处理微型或异形O型圈。
典型设备:真空吸盘机械手、高精度吸附平台。
1.4、热装配设备
工作原理:加热O型圈或工件,利用热胀冷缩原理实现装配。
特点:
适用于过盈配合或硬质材料(如氟橡胶O型圈);
需精确控制温度,防止材料老化。
典型设备:恒温加热装配台、红外线热装系统。
1.5、机器人集成装配系统
工作原理:工业机器人搭载定制夹具(如柔性夹爪、视觉引导系统),完成O型圈抓取、定位和装配。
特点:
灵活适配多规格O型圈;
支持复杂路径规划和多工位协同。
典型设备:六轴协作机器人工作站、SCARA机器人装配线。
1.6、综合装配检测一体机
工作原理:集成装配与检测模块(如机器视觉、气密性测试),实时反馈装配质量。
特点:
实现装配过程闭环控制;
减少人工复检环节,提升良品率。
典型设备:在线式检测装配机、气密性测试装配一体机。
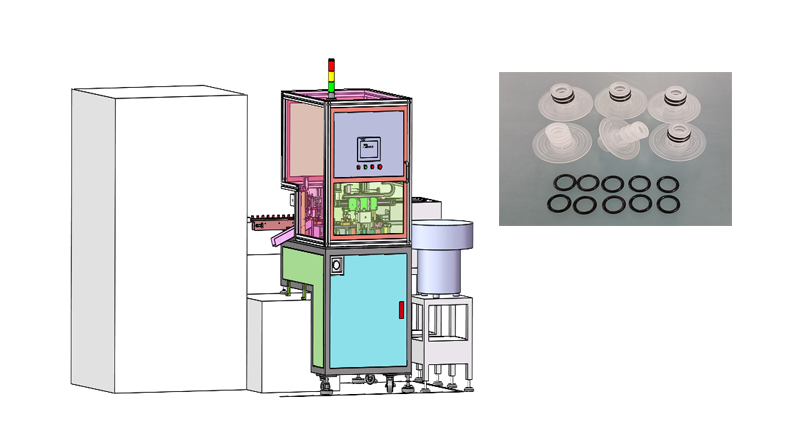
二、应用场景
2.1、汽车制造
场景需求:发动机密封件、油管接头O型圈装配,要求高稳定性与耐油性。
适配设备:伺服压装机、机器人集成系统(配合力控传感器)。
2.2、电子电器
场景需求:连接器、电池组密封圈装配,需防静电且避免划伤。
适配设备:真空吸附设备(配防静电吸盘)、微型推装机械手。
2.3、医疗器械
场景需求:注射器、输液管密封圈装配,需无菌环境与高洁净度。
适配设备:全封闭式真空吸附系统(带洁净室适配功能)。
2.4、航空航天
场景需求:耐高温/高压密封圈(如液压系统),装配精度要求极高。
适配设备:热装配设备(控温精度±1℃)、六轴机器人(配激光定位)。
2.5、工业阀门与管道
场景需求:大型O型圈(直径>50cm)装配,需大负载设备。
适配设备:重型液压推装机、定制化机械臂(扩展臂展)。
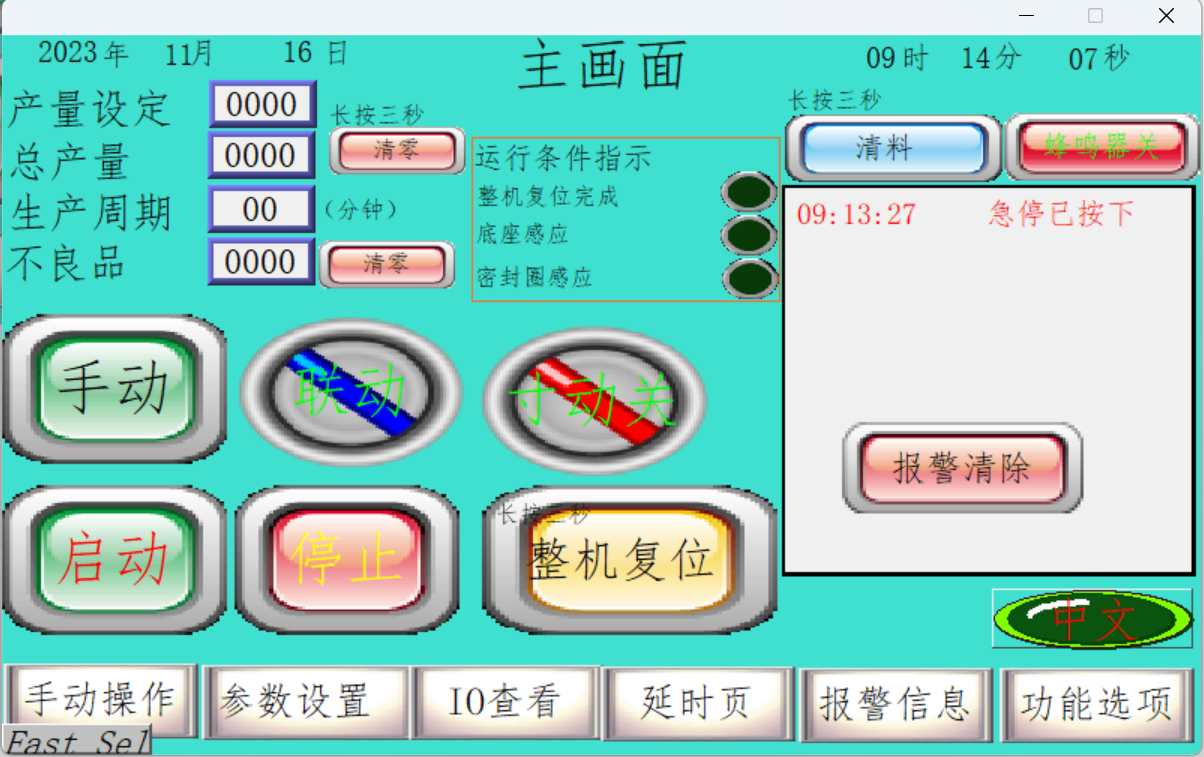
三、使用要求
3.1、O型圈材料适配性
根据材质(如NBR、硅胶、氟橡胶)调整装配参数(压力、温度);
硅胶等软质材料需降低吸附或夹持力度,防止变形。
3.2、装配精度控制
位移精度:通常需控制在±0.05mm以内;
压装角度偏差:避免倾斜导致O型圈扭曲(需夹具导向设计)。
3.3、环境适应性
洁净车间:医疗、电子领域需配置无尘罩或HEPA过滤系统;
防油防尘:汽车、重工业场景需设备IP防护等级≥IP54.
3.4、设备兼容性
支持多规格O型圈快速换型(如模块化工装、参数记忆功能);
与生产线节拍匹配(如汽车行业要求节拍≤3秒/件)。
3.5、质量检测集成
装配后需自动检测O型圈位置(视觉系统)或密封性(气密性测试);
数据可追溯,支持MES系统对接。
3.6、安全与维护
设置急停装置与安全光栅,防止夹伤风险;
定期保养真空发生器、气动元件,避免气压不足导致装配失效。
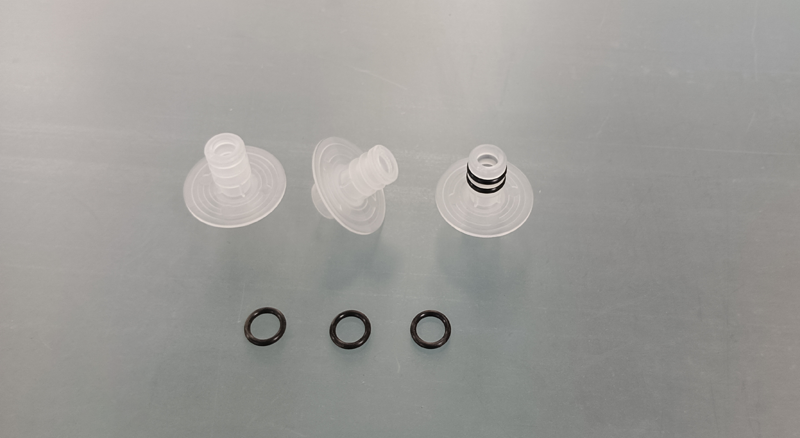
四、总结
O型圈自动化装配设备类型多样,需根据具体场景选择:
大批量生产(如汽车):优先机器人集成系统或伺服压装机;
高洁净需求(如医疗):真空吸附设备+封闭式工作站;
复杂工况(如高温装配):热装设备+温度闭环控制。
关键建议:
引入前需明确O型圈规格、材料特性及产量需求;
进行工艺验证(如试装配50-100件),优化参数;
选择支持柔性化升级的设备,适应未来产品迭代。
通过合理选型与规范操作,自动化设备可显著提升O型圈装配效率(约提升50-80%),同时降低不良率至0.1%以下。