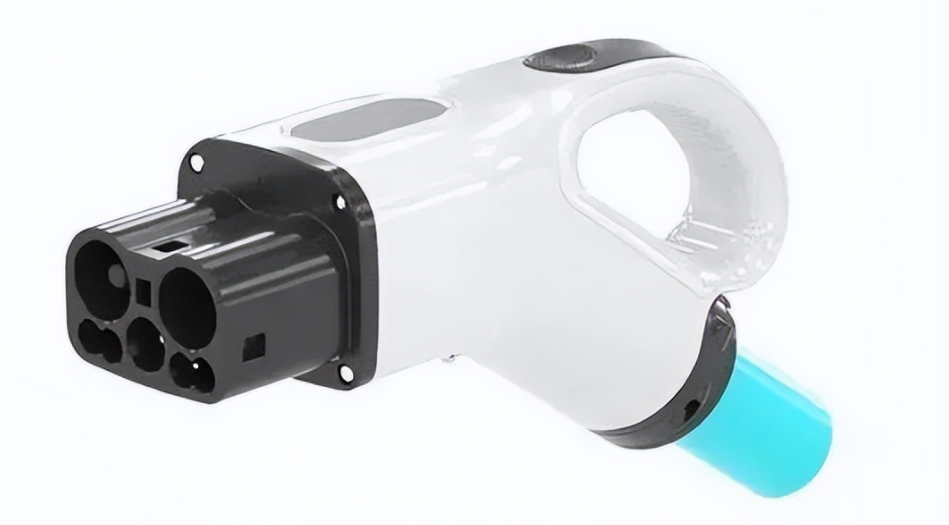
一、交直流充电口自动化组装生产线的设计目标
1、高效生产:通过全自动化流程实现24小时连续作业,单件组装时间≤30秒,产能≥1500件/日。
2、高精度装配:采用视觉定位系统(重复定位精度±0.02mm)确保充电接口的金属触点、绝缘层等关键部件精准装配。
3、柔性兼容:支持AC(Type1/Type2)和DC(CCS/CHAdeMO/GBT)多种接口规格的快速切换。
二、交直流充电口自动化组装生产线的系统构成
2.1、核心设备
A、六轴机械臂(负载≥10kg,臂展1.2m)
B、高精度伺服压装系统(压力控制范围0.1-50N)
C、红外热成像质量检测模块
2.2、智能控制系统
A、PLC(西门子S7-1500系列)+MES生产管理系统
B、机器视觉系统(500万像素工业相机)
2.3、物料输送
A、振动盘定向供料系统
B、AGV自动送料车(载重500kg)
2.4、技术特点
A、模块化设计支持快速换型(换型时间≤15分钟)
B、集成工业物联网(IIoT)实现生产数据实时监控
C、不良品自动分拣率≥99.5%
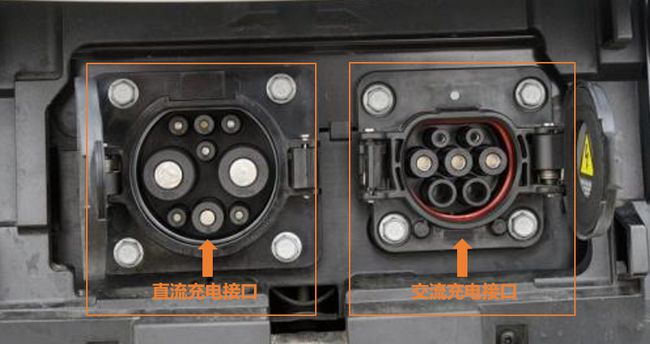
三、交直流充电口自动化组装生产线的自动化组装流程
3.1、零部件上料
A、振动盘自动分选端子/外壳(节拍5秒/件)
B、AGV输送PCB板至装配工位
3.2、精密压接
A、伺服压机完成铜端子与线缆压接(压力监控±0.5N)
B、视觉系统检测压接深度(公差±0.1mm)
3.3、绝缘装配
A、机械臂抓取硅胶密封圈(抓取精度±0.05mm)
B、热熔工艺固定绝缘层(温度控制150℃±2℃)
3.4、外壳组装
A、自动涂胶系统施加UV胶(胶量控制0.1ml±5%)
B、气动夹具完成外壳扣合(压力300N±10N)
3.5、电气测试
A、自动插拔测试(1000次循环,插拔力检测5-80N)
B、耐压测试(AC 2500V/60s,漏电流≤10mA)
3.6、激光打标与包装
A、光纤激光器标记产品信息(深度0.2mm)
B、机械手自动码垛(堆叠高度误差≤0.5mm)
3.7、关键参数控制
工序 | 控制参数 | 标准范围 | 检测方式 |
压接 | 压力值 | 25N±0.5N | 压力传感器 |
涂胶 | 胶量 | 0.1ml±5% | 称重传感器 |
耐压 | 绝缘电阻 | ≥100MΩ | 高压测试仪 |
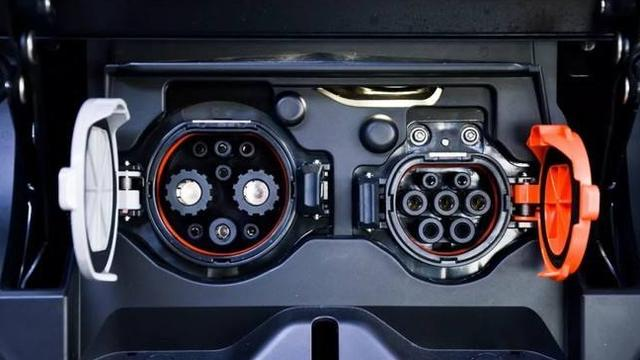
四、交直流充电口自动化组装生产线的使用注意事项
4.1、人员防护
A、进入机械臂工作区需佩戴安全光栅钥匙
B、高压测试区域设置双层互锁防护门
4.2、设备安全
A、每日开机前检查急停按钮功能
B、禁止在湿度>80%RH环境下运行激光设备
4.3、维护保养要求
4.3.1、定期维护
A、每500小时更换直线导轨润滑脂(ISO VG32)
B、每季度校准视觉系统标定板
4.3.2、耗材管理
A、UV胶需避光储存(温度15-25℃)
B、压接模具寿命预警设定为50万次
4.4、故障应急处理
4.4.1、常见问题
A、端子卡料:立即触发急停,使用专用退料工具处理
B、压力异常:检查气压源(要求0.6MPa±0.02)及伺服阀反馈信号
4.4.2、数据追溯
A、MES系统自动保存最近72小时工艺参数
B、质量数据保留周期≥5年
五、技术优势总结
5.1、较传统产线提升效率300%,人工成本降低70%
5.2、通过IATF 16949体系认证,CPK值≥1.67
5.3、支持与新能源整车厂MES系统无缝对接